できるだけ少ないエネルギーでガラスを製造することが競争力向上につながる
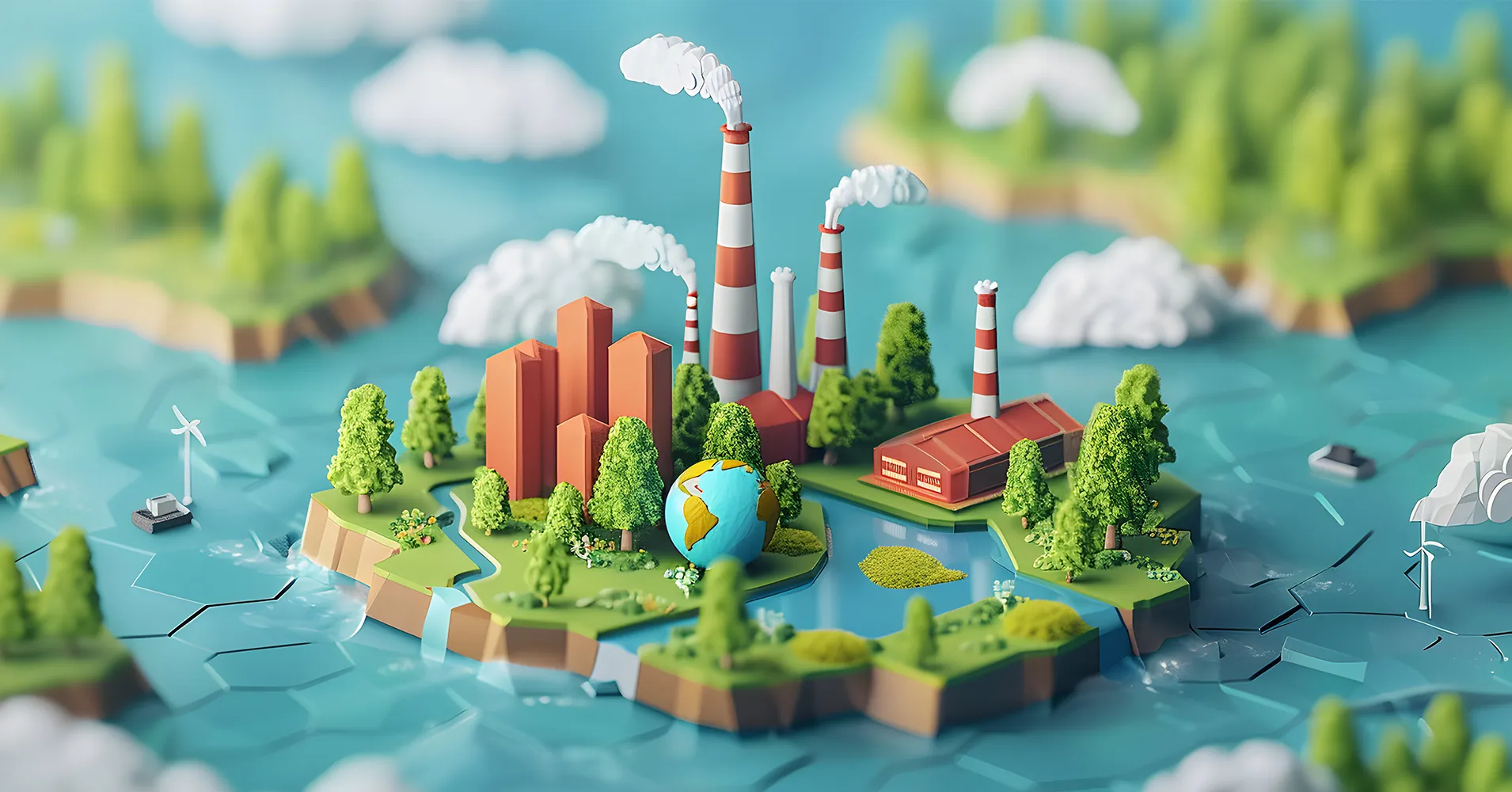
地球規模の課題である気候変動問題の解決に向けて、日本政府は2050年までに温室効果ガスの排出を全体としてゼロにする「カーボンニュートラル」を目指すことを宣言しました。現在120を超える国と地域が同様の目標を掲げており、企業において持続可能なビジネスモデルを構築するにあたってカーボンニュートラルを目指す取り組みは世界的な課題となっています。
日本電気硝子(NEG)でも、2050年までにカーボンニュートラルを達成するという目標(2022年2月公表)を掲げて様々な取り組みを行っています。
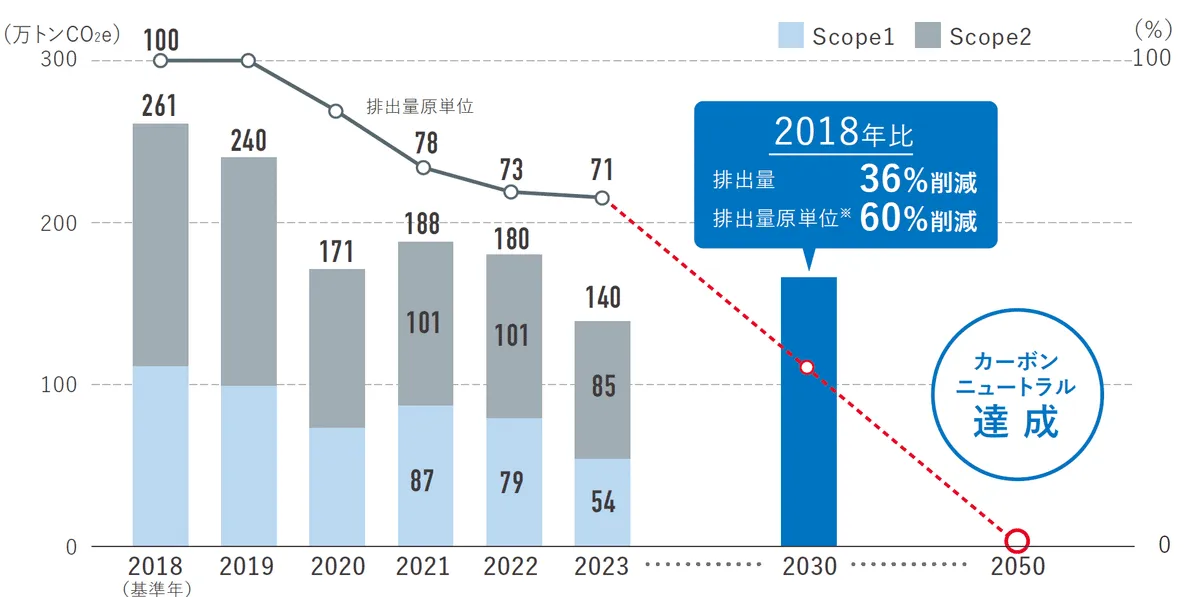
Scope 1(直接排出):企業が直接管理している資産からの温室効果ガス排出量。
Scope 2(間接排出):企業が購入したエネルギー(主に電力)の使用に伴う間接的な温室効果ガス排出量
「自然との共生」を大切な価値観として掲げ、時代に先駆けていち早く環境保全に取り組んで来たNEG。その背景や、カーボンニュートラル達成のために何が行われているのかなどについて、山崎博樹(やまざき ひろき)取締役常務執行役員(環境担当)と金谷 仁(かなやひとし)常務執行役員(プロセス技術担当)に話を伺いました。
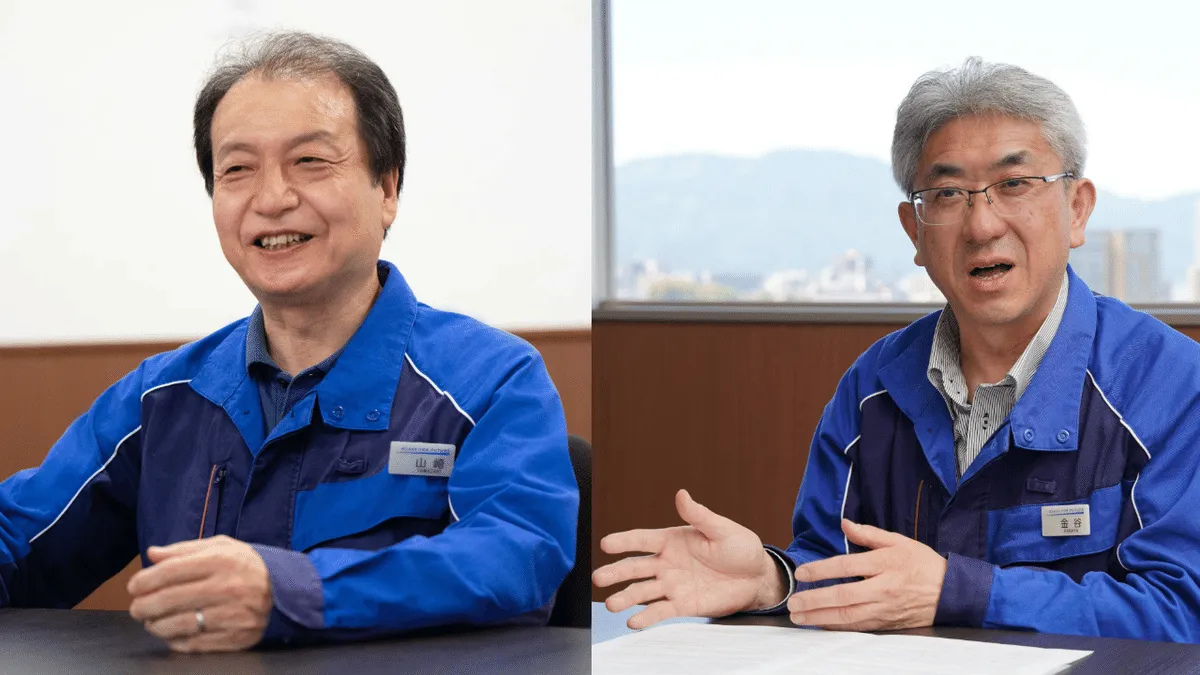
高度経済成長期の光と影
NEGの創立は、戦後の混乱がまだ残る1949年。その後、日本は1955年頃から高度経済成長期に突入し、1970年代はじめにかけて急速に経済が成長・発展する一方で、この間に各地では公害問題が顕在化していきました。NEGでも環境問題を引き起こした苦い過去があります。
山崎 「ガラスは、いろんな元素を溶かし込むことができ、それによって様々な機能を発現させることができるという特徴があります。かつては、その目的のためにガラスには、環境負荷物質や人体にとって好ましくない影響を及ぼす物質も用いられてきました。その代表的なものとして、鉛やフッ素、ヒ素、ホウ素などがあります。当時は、ガラスの特性を重視し、優れた機能を発現する有用な物質として、これらを積極的に用いたガラスが製造されました。もちろん、法令や環境規制は遵守していましたが、当時の環境規制の基準は今とは比べ物にならないくらい低いレベルであり、排ガスや排水、廃棄物に対する企業の意識も決して高いとはいえない時代背景の中で、意図に反して周辺環境を汚染してしまうという結果を引き起こした時代といえます。
当社でもこの時期において、滋賀高月事業場の排ガスに含まれていたフッ素化合物が地元養蚕農家のカイコのエサとなる桑の葉に影響を与え、カイコが繭を作らないという事態や、藤沢事業場(2015年閉鎖)で使用していた鉛やフッ素が周辺環境を汚染しているとして住民運動に発展し、稼働中であった溶融炉の半数を停止せざるを得ないという経験をしました。」
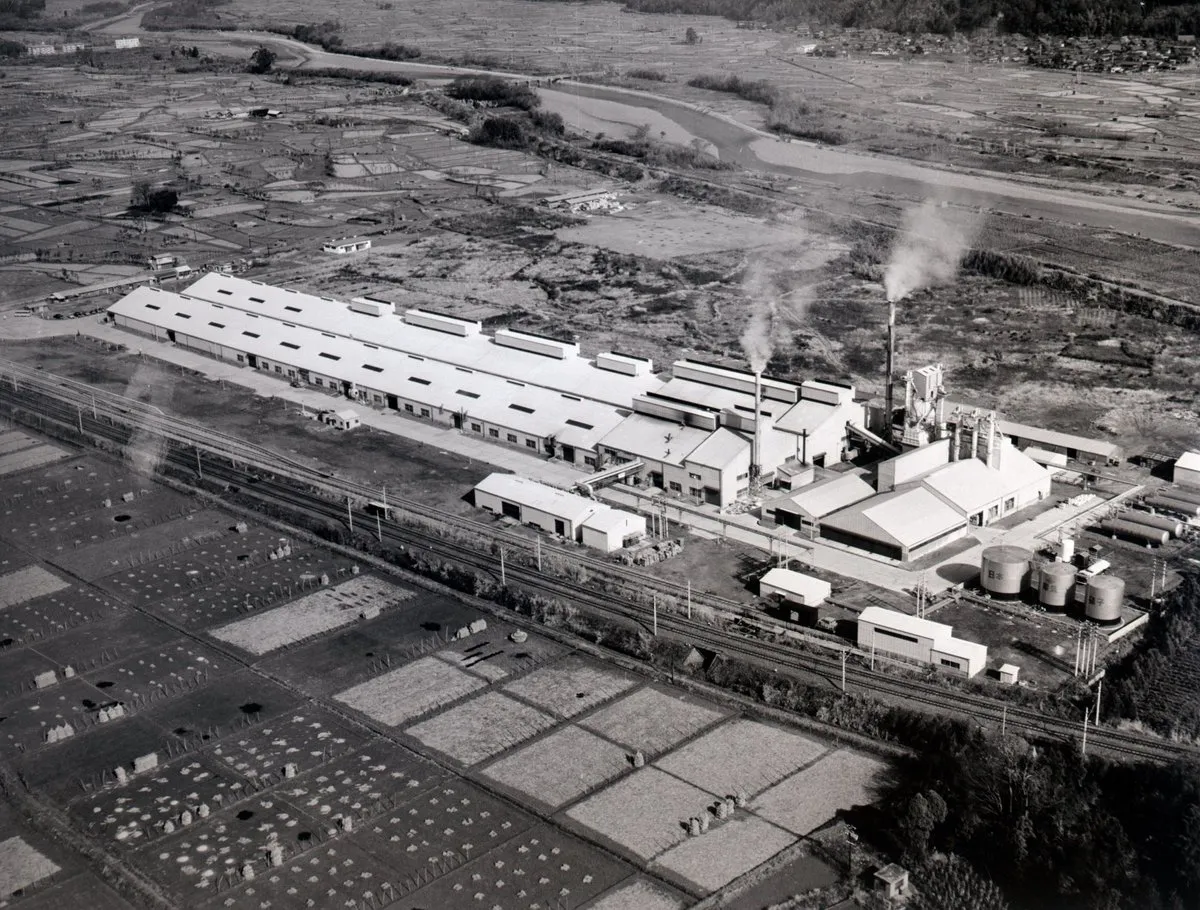
1970年代から始まったサステナブル経営
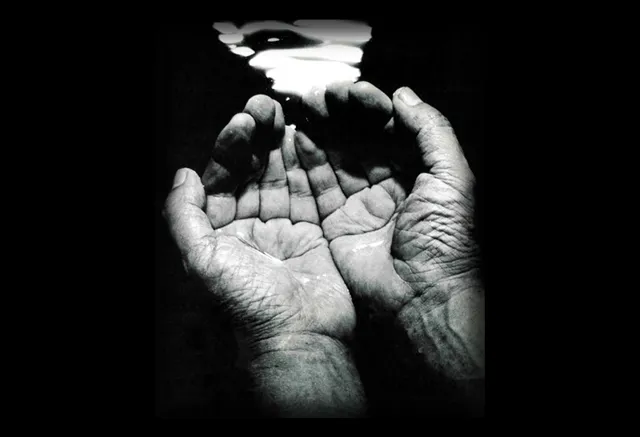
出典:技術PR誌「P&P」2号 発行年:1976年 発行所:日本電気硝子株式会社
昨今はどの企業でも環境負荷をできるだけ小さくする事業運営が主流となっていますが、NEGでは、上記の苦い経験の上に立ち、今の世の中の動きに先駆けて1970年代からサステナブルな経営の取り組みをスタートしました。
山崎 「当時の社長(実質的な創業者である3代目社長 長崎準一氏)は『場当たり的に環境ルールを守るという姿勢での経営では、会社は存続できない』として、ある程度コストを犠牲にしてでも、できるだけ少ない原料や水、エネルギーでムダなく生産をする(インプット・ミニマム)とともに、外部への環境影響物質の排出を最小化する(アウトプット・ミニマム)ことを実現するために必要な設備を整えていくことを強く指示されました」
NEGの主力拠点が集まる滋賀県という自然豊かな地で事業を継続していく上で、地域の住民の方たちとの連携は極めて重要な課題となります。NEGでは、地域住民の方々が満足するレベルまで周辺環境への影響を最小化する取り組みを粘り強く続けてきました。
山崎 「上述のとおり、インプットとアウトプットをそれぞれミニマムにしていく取り組みは、1970年代から今に至るまで一貫して続けてきたことです。近年、SDGsという言葉が登場したことにより、昔から当社では当然のこととしてやってきたことが、いま世間で騒がれています。一見すると当社がこれまで行ってきたことが先見的な取り組みであるように見えるかもしれませんが、我々にとっては、何ら珍しいことでもないのです。」
山崎 「廃棄物を例にとってお話しましょう。ガラスの世界では、製造に伴う副生成物は元々ガラス原料を構成していたものが大半であり、不要なものを除去すれば、再びガラス原料として用いることができます。例えば、ガラスを研磨した際に生じる廃研磨材(スラッジ)はそのまま使えばガラスを着色してしまいますが、鉄分を除去すればガラス原料として使用することができ、天然原料の使用量を削減できます。また排ガスに含まれる粉塵も、ちゃんと集めて適切な処理をすれば、再びガラス原料として再生できます。ガラスにはこのような特徴があることを当時の長崎社長が強く意識され、一般的にリサイクルへの取り組みが積極的でなかった時代から、強い意志を持ち、費用と手間をかけてもガラスの原料に戻す、ということに地道に取り組み、今に至っています」
世の中の動きに先んじて、廃棄物・排ガスの徹底したリサイクルに長年にわたって取り組んできたことが今日にNEGの姿に繋がっているということですね。
インプット・ミニマムの道はカーボンニュートラルに通ずる
ガラスの製造では、とりわけ原料をガラスに溶融する工程で多くのエネルギーを必要とします。したがって溶融炉から排出される温室効果ガスの削減が重要な課題となります。
そこでカギになるのが、溶融工程でのエネルギー効率の向上とCO₂排出量の削減への取り組みです。NEGではこれまで具体的施策として、以下の3つを積極的に展開してきました。
-
酸素燃焼炉の導入
-
溶融炉の燃料転換
-
溶融エネルギーに係る電力比率の向上
1. 酸素燃焼炉とは燃料の燃焼に空気ではなく酸素を用いる方式のことで、1993年に当社が日本で初めて導入し、使用エネルギー量・CO₂排出量・窒素酸化物(サーマルNOx)の削減を実現しています。
2.溶融炉の燃料転換では、長らく用いていた重油から、よりCO₂排出量が少ない天然ガスへ切り替えを進め、すべての溶融炉で切り替えが完了しています。
3.電力比率の向上については、溶融炉内に電極を挿入し、直接ガラスに通電・加熱することにより、熱伝達効率が大幅に向上し、使用エネルギーの削減が行えます。
山崎 「例えば、ガラス溶融の燃料として重油を使うと、CO₂に加えて大気汚染の原因となるSOx(硫黄酸化物)が発生します。NEGでは2010年度に重油の使用を完全に廃止したことで、CO₂排出量の削減に加え、大気汚染物質の排出を大幅に抑制しました。また、従来の空気を用いる燃焼方式では、空気の約70%を占める窒素ガスは燃焼には寄与せず、溶融炉で加熱され、大事な熱を炉の外に持ち出します。酸素燃焼方式では窒素が炉内に持ち込まれないため、エネルギー効率が大幅に向上するだけでなく、窒素の加熱により生じ、大気汚染の原因となるNOxの発生も抑制できます。現在では、さらに一歩進めて燃焼時にCO₂が発生しない技術として、水素を燃料とする燃焼方式の開発を進めています。こういった努力を続けることで、年々CO₂排出量を減少させることを実現しています」
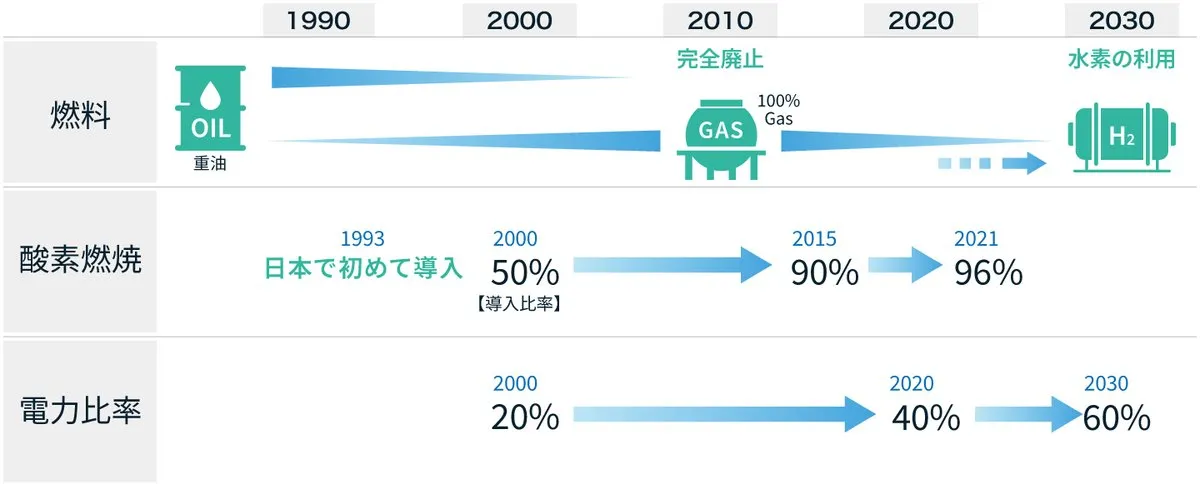
しかし、環境という側面に力を注ぎ過ぎる余りに、肝心の製品競争力が他社より劣ってしまっては意味がありません。
山崎 「できるだけ少ないエネルギーでガラスを製造することを目指せば、当然製造コストは下がり、同時にCO₂排出量も削減できる、ということでインプット・ミニマムに徹したモノづくりが、当社製品の競争力向上とカーボンニュートラルにつながっているということです」
NEGは世界一効率の高いモノづくりこそが、世界一環境にやさしいモノづくりにつながるという考えのもと、品質や歩留まりの向上を通じて省エネルギーやCO₂排出削減に取り組むサステナブルなものづくりを実践しています
さらなる飛躍を目指して、全電気溶融炉への転換
前述のとおり、NEGの溶融炉では、天然ガスを用いた酸素燃焼による間接的な加熱に加え、溶融炉内に挿入した電極を用いて直接ガラスに通電して加熱する、直接通電加熱を組み合わせたハイブリッド溶融炉を積極的に展開してきました。現在ではそこからさらにワンステップ上のアプローチとして、溶融に必要なエネルギーをすべて電気でまかなう全電気溶融炉への転換も進めています。2023年の時点で、当社グループにおける電気エネルギーの導入比率は39%に達し、今後も積極的に転換を進めていこうとしています。
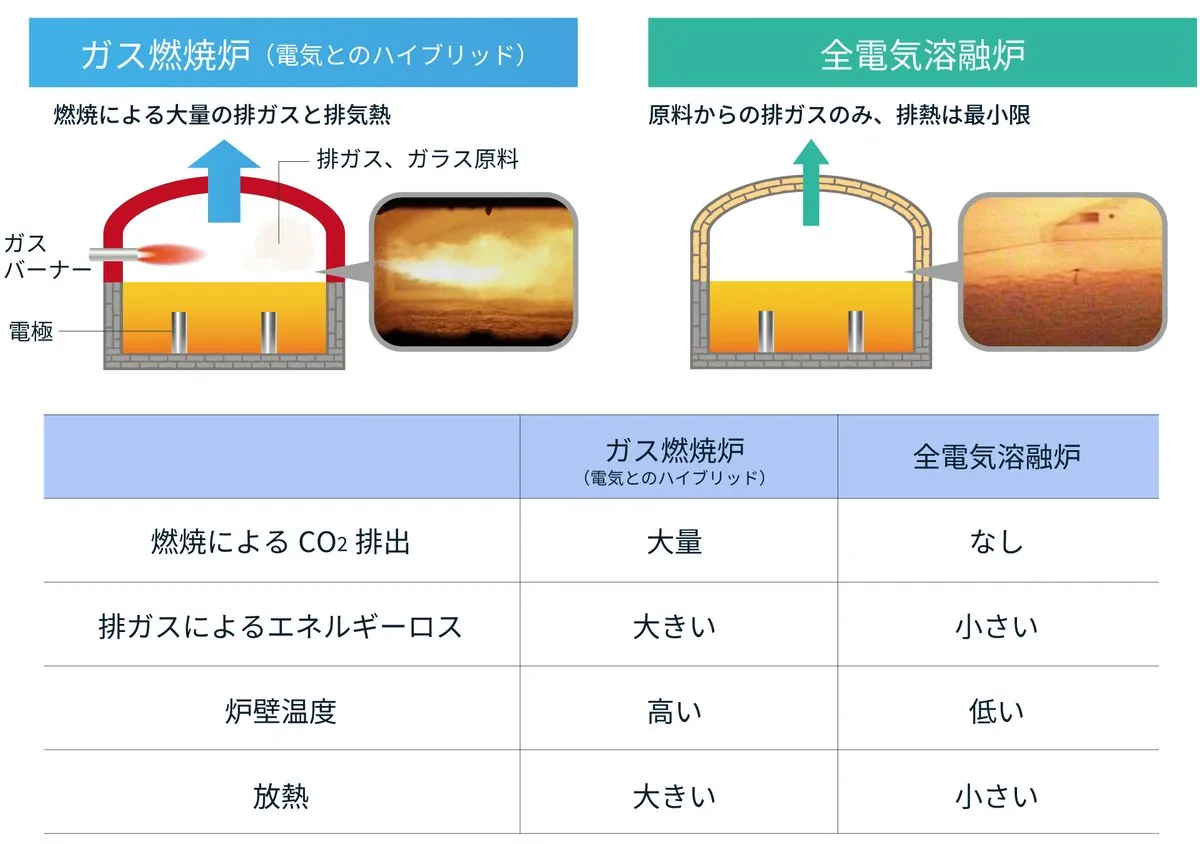
山崎 「NEGではガラス溶融に必要なエネルギーを基本的にすべて電気によってまかなう全電気溶融炉を業界に先駆け、1974年に導入しました。重油やガスなどの燃料を燃やさないため、燃焼に起因する排ガスを出さない、騒音を出さないといったメリットがあります。残された課題もありますが、全電気溶融はカーボンニュートラルを実現する上で重要な技術です。
かつては、全電気溶融に適するガラスの種類も限られ、またその技術もまだまだ未熟であったこともあり、コストが燃焼炉のそれには追い付いていなかった部分もあって、細々と取り組んできたところが、ここ10年ほどの間に溶融炉内部での溶けたガラスの流れなどを推定するためのシミュレーション技術をはじめ、周辺技術が飛躍的に進化してきたことにより、本格的に全電気溶融技術を展開することができるようになりました。
今日、カーボンニュートラルがクローズアップされるようになったがゆえに、当社でも突然全電気溶融を推進し、カーボンニュートラルにつなげようとしたわけではなく、長年にわたりインプットとアウトプットをミニマムにすることを目指して地道に取り組んできた我々の道のりが、時代が求める方向性と合致していたということだと思います」
2050年を見据えた全電気溶融炉への全面切り替えは可能?
NEGにおける全電気溶融炉への切り替えは着実に進んでいますが、クリアすべき課題も残っています。
金谷 「将来的にすべて全電気溶融炉にしたいと考えておりますが、現時点ではガラスの種類や生産の規模によって向き不向きがあります。単純に原料を溶かすだけであれば全電気溶融で対応が可能ですが、求められる品質やコストに見合った生産ができるかと言えば、話が変わって来るというのが現状です。我々が目指しているのは競合よりも良い品質のガラスを、より低いコストで効率良く生産する、しかもその先がカーボンニュートラルにつながっているということ。これを実現できる技術が全電気溶融ということです」
全電気溶融炉にすべてを置き換えるまでの間、燃焼に依存せざるを得ないところへの対処はどうでしょうか。
金谷 「先ほども言及があったように、現時点でどうしても燃焼に頼らざるを得ないところには、燃焼時にCO₂が発生しない技術の開発を進めています。2022年度には水素100%を燃料とした水素-酸素燃焼バーナーを開発、ガラス溶融の実証実験に成功しました」
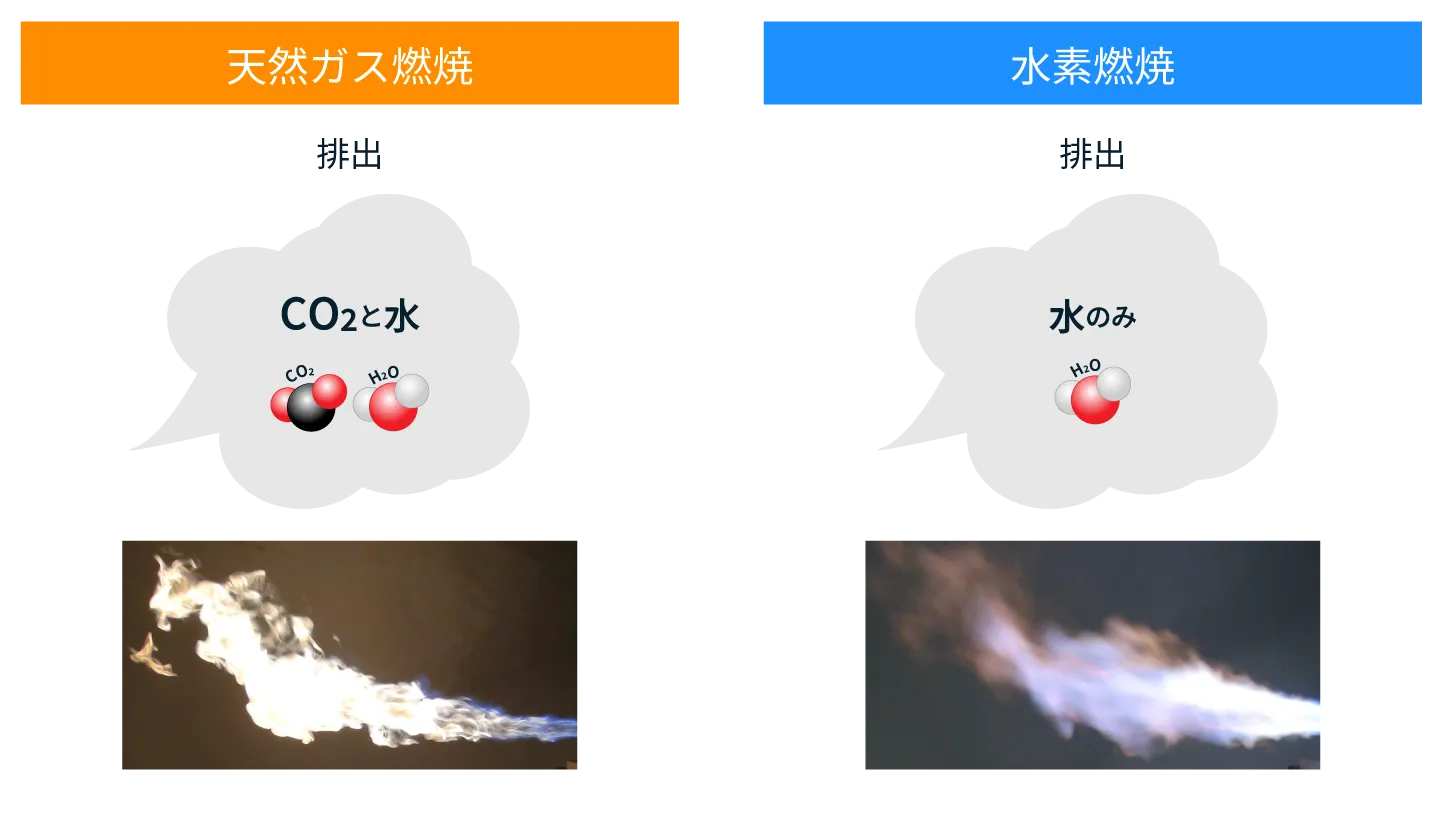
またNEGでは、使用電力の一部に再生可能エネルギーを使用することによるCO₂排出削減にも取り組んでいます。例えば、滋賀高月事業場内に大規模な太陽光発電設備(年間 約3.7GWh想定)を設置し、2023年4月から本格稼働を行っています。
「世界一効率の高いモノづくりこそが、世界一環境にやさしいモノづくりにつながる」との確固たる考えのもと、2023年度には、2018年比でエネルギー使用原単位*を21%低減させるなど、エネルギーの効率的な使用とムダの削減に継続して取り組むNEG。1970年代から一貫して続けてきたインプットとアウトプットをそれぞれミニマムにしていくNEGのサステナビリティ経営への取り組みは、2050年のカーボンニュートラル達成という目標に向けて確実な歩みを進めています。具体的な取り組み内容や各種データなどは当社Webサイトのサステナビリティページの「統合レポート」や「ESGデータブック」で公開しております。ぜひ、そちらもご覧ください。
-
●エネルギー使用原単位*: 単位重量の製品を生産するのに必要なエネルギー使用量