セラミックス貢献賞受賞者に聞くNEGが育む技術力の根源
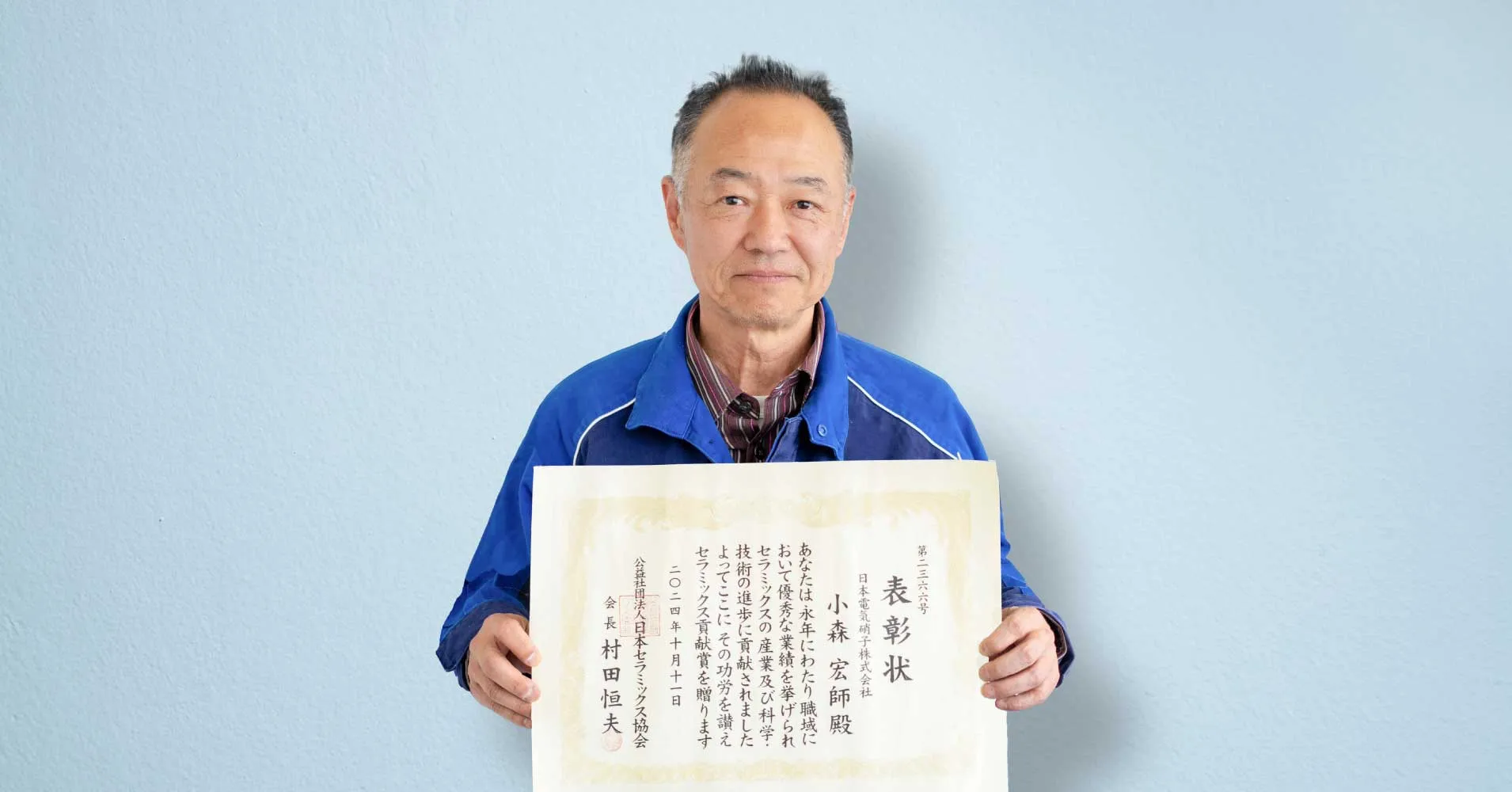
セラミックス分野で優れた功績を上げた個人を毎年表彰する、公益社団法人日本セラミックス協会主催の2024年度(第58回)セラミックス貢献賞が発表され、日本電気硝子株式会社(以下、NEG)の小森宏師さんが受賞しました。
読者の中にはガラスメーカーのNEGからセラミックス分野での受賞者が輩出されたことに意外な印象を持った方もいるのではないでしょうか。セラミックスは無機固体材料の総称です。シリコンやセメント、陶磁器のイメージが強いですが、実はガラスもセラミックスに分類されます。NEGは過去にもセラミックス貢献賞を複数回受賞してきました。
今回はセラミックスに関連する製造現場および研究開発、試験・分析現場において技能業務に長年従事し、成績優秀かつ技能抜群の者が対象となる技能部門を受賞した小森さんにお話を伺いました。
小森さんは1984年(昭和59年)にNEGに入社。ガラス特性の測定技術開発に関わり、ブラウン管(CRT)用ガラスの組成開発、CRT用ガラスや液晶ディスプレイ(LCD)用ガラス生産の海外進出におけるガラス物性測定装置・調合プラントの仕様・製作支援、CRT用ガラス・プラズマディスプレイ(PDP)用ガラス・LCD用ガラスの材質管理、調合工程での生産活動に従事されました。近年は後任の指導にも注力し、2025年からは環境部へ異動し業務を行っています。
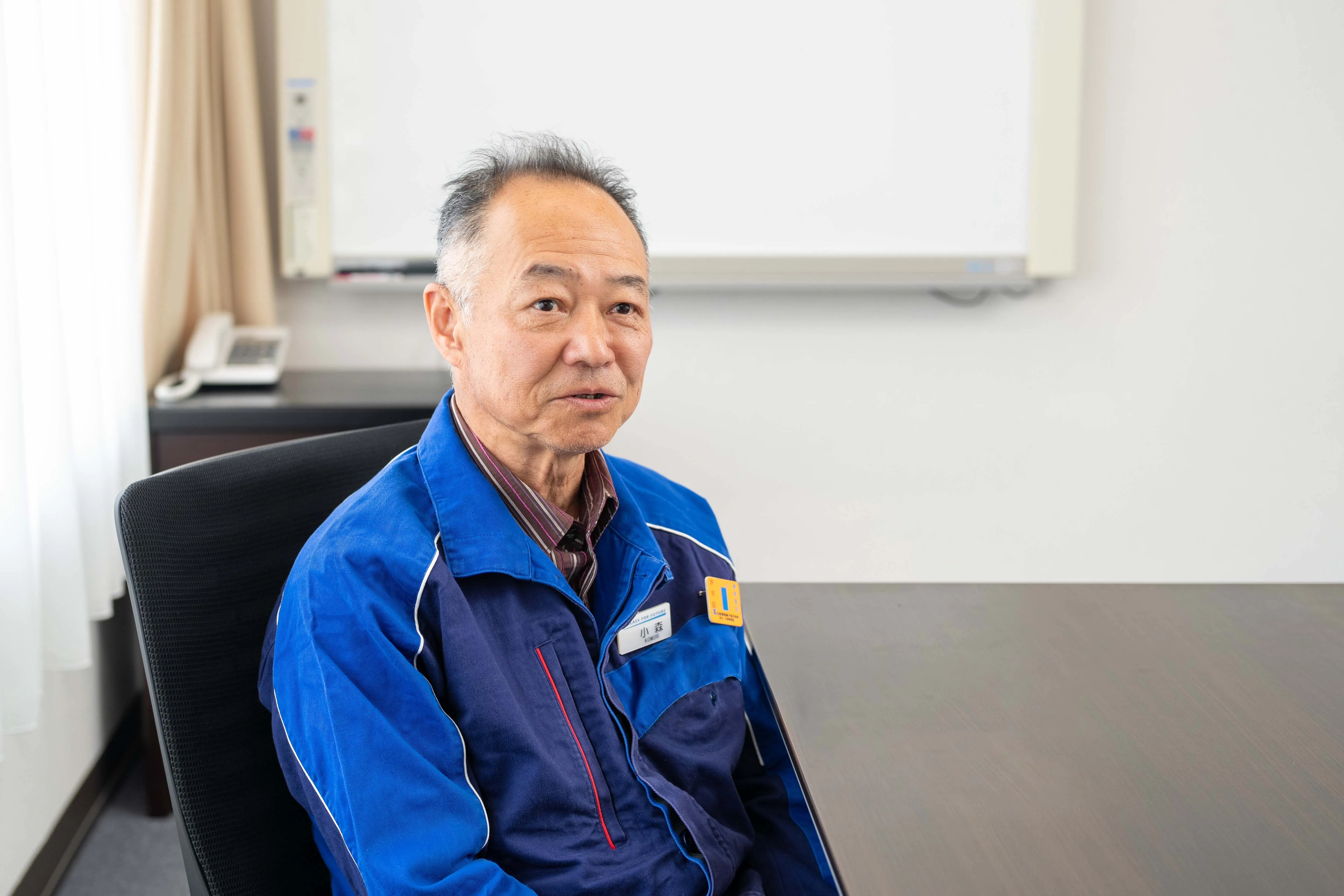
技術者としてゼロからのスタート
――小森さんがNEGでガラス特性の測定技術開発に携わった背景を教えてください。
小森さん「私がNEGに入社したのはいわゆるバブルの時代の少し手前で、景気が拡大傾向にあった時期です。技術部第二技術課という部署で、ガラス特性の測定技術開発に携わりました。簡単に言うとガラスの物性を測定する装置を作る仕事です。この業務を10年間担当することになります。
入社当時の私は、ガラスの特性もよく理解できておらず、それどころか電気や機械などの知識もありませんでした。当時はPCでプログラミング言語のBasicを使って、装置の運転用ソフトを作っていましたが、私はPCやプログラミングの知識もまったく持っていませんでした。装置を作るための図面の書き方も分かりませんでした。すべてにおいてゼロからのスタートだったのです。
ガラスの特性やプログラミングの知識などは、上司が1つずつ教えてくれました。プログラミングの学習はまず時計を作るところから始めたことを覚えています。
――ガラスメーカーであるNEGが、自社で測定装置を開発する理由はどこにあるのでしょうか?
小森さん「NEGは特殊ガラスのメーカーです。ガラスは非常に自由度の高い素材で、材料設計や製造プロセスを工夫することで、さまざまな特性を持たせることができます。たとえば、紙よりも薄くしなやかに曲がるガラスや、急激な温度変化に耐えられる超耐熱ガラスなどがあります。
こうした特性を備えたガラスを製品として提供するには、その性能を正確に測定し、確かな根拠として示すことが不可欠です。だからこそ、私たちはガラスを測定することと、その精度を高めることを重要視しています。
しかし、そうしたガラスの物性を測定する装置は、市販されているものがほとんどありません。かろうじてガラスの透過率を測る装置が存在するくらいでしょうか。ガラスの粘性や膨張率、電気特性を測る装置は特殊過ぎてどこも製作しておらず、外部から装置を買うことができないので、自分達で作るしかありませんでした。測定方法は国際基準で決まっているので、その基準に準じて製作しました。
最初からすべてを自分で手がけたわけではありません。はじめは直属の上司が作ったものに、測定精度や効率の向上が図れる工夫を盛り込むなどして、ブラッシュアップをしていきました。」

――測定精度を高める上で、特に難しい点はありますか?
小森さん「ガラスの特性を測定する際は、常温ではなく高温下で行うことが多く、その高温環境で正確に測定を行うこと自体が非常に難しいです。たとえば、1,000℃まで加熱して測定を行う場合、ガラス試料全体の温度を均一に保つ必要があります。温度にムラがあると、正確なデータが得られないからです。また、熱膨張を測定する際には、ガラスそのものだけでなく、それを支える周囲の部材も同じく膨張します。そのため、周辺部材の影響を考慮しなければなりません。
さまざまな改善を続けながらいろいろと学び経験を積んだおかげで、新たな特性を測りたいというニーズが持ち込まれても、それを測定する装置を製作することができるようになりました。そして数年後には、完成品を海外のガラスメーカーに販売・輸出していました。」
――装置を作るだけでなく海外へ販売もされていたのですね。それはどういったお仕事だったのでしょうか。
小森さん「私が入社した頃、NEGでは調合・溶融・成形までの設備一式を海外企業に販売するビジネスも展開していました。その中のラボラトリーとして、品質管理のための測定装置も含まれており、その製作を担当しました。
また、1990年代初頭にNEGが海外での生産を本格化させた際には、マレーシアやイギリスのウェールズ(NEGUK)(現在は閉鎖)、さらに中国や韓国の工場にも測定装置を導入しました。
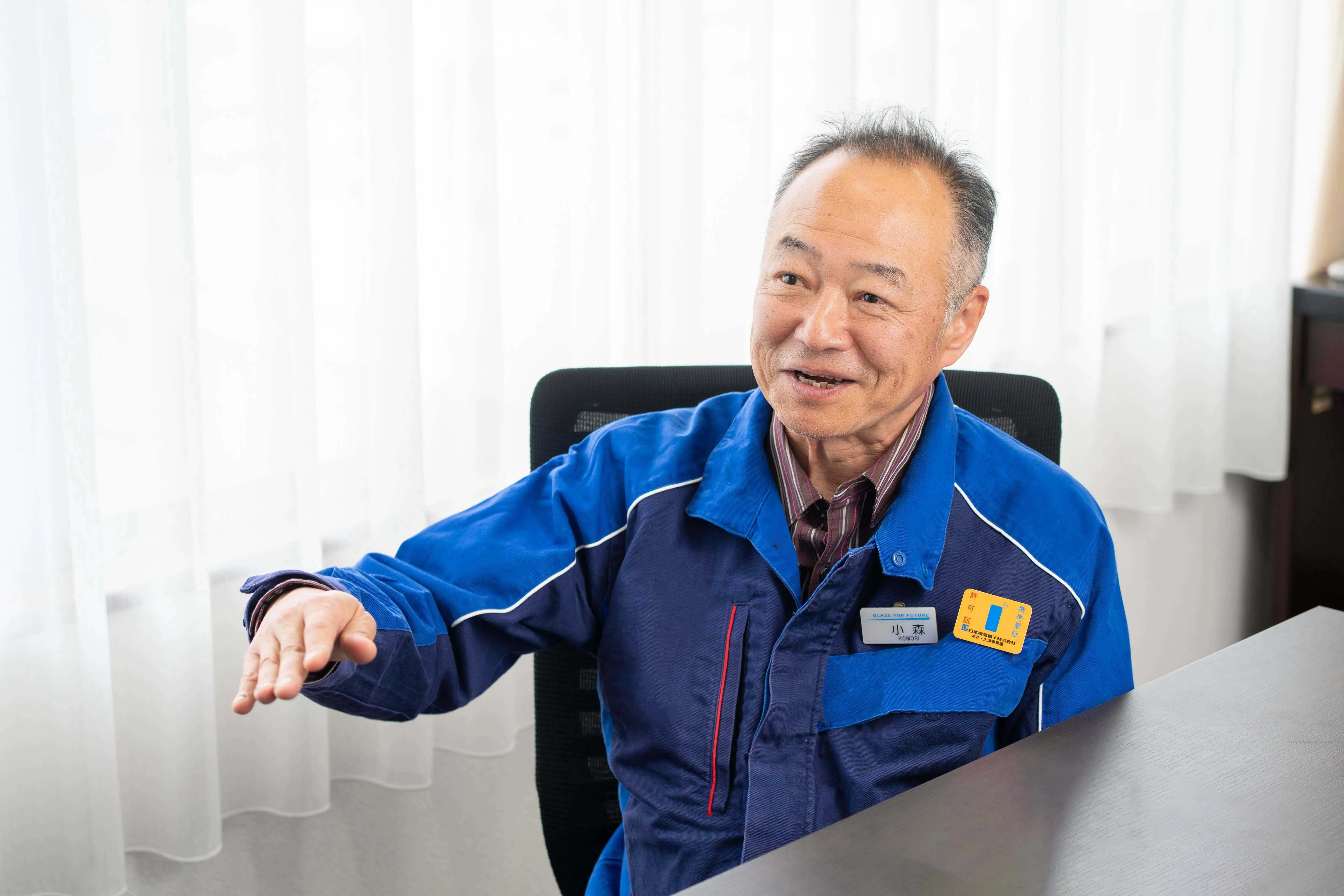
品質を保ちながらコストを見直す取り組み
――CRTからフラットパネルへの移行期にCRT用ガラスの組成開発をご担当されていたそうですが、どのような工夫や苦労がありましたか。
小森さん「私が担当していた「ディスプレイ」といえば、今はLCDがその代名詞となっていますが、私が入社した頃はCRTのことを指しました。NEGは、この事業を私が担当するずっと前、1965年(昭和40年)から手掛けていました。
私がCRT用ガラスの組成開発を担当した1995年には、すでに30年近い実績がありました。そのため、生産コストを1円でも下げるためのコストダウンが業務の中心でした。つまり、できるだけ安価な原料を用意して、その中でどう品質を確保するかを模索していました。
また、リサイクルで市場から集めたCRT用ガラスを窯に戻して溶かし、再利用することによるコストダウンにも取り組みました。
リサイクルカレットに限らず、さまざまなものを試し、その使い方を考え、どれだけコストが下がるか探っていて、例えば研磨したあとの廃液まで試しました。ガラスを鏡面に磨くときに使う『酸化セリウム(cerium oxide)』は、実はCRT用ガラスの必要成分なのです。そのため、研磨の廃液がセリウム源として再利用できれば、大きなコストダウンにつながるのではないかと考えました。このようにあらゆるリサイクル手段を模索しながら、CRT用ガラス事業の生き残りに奮闘していました。
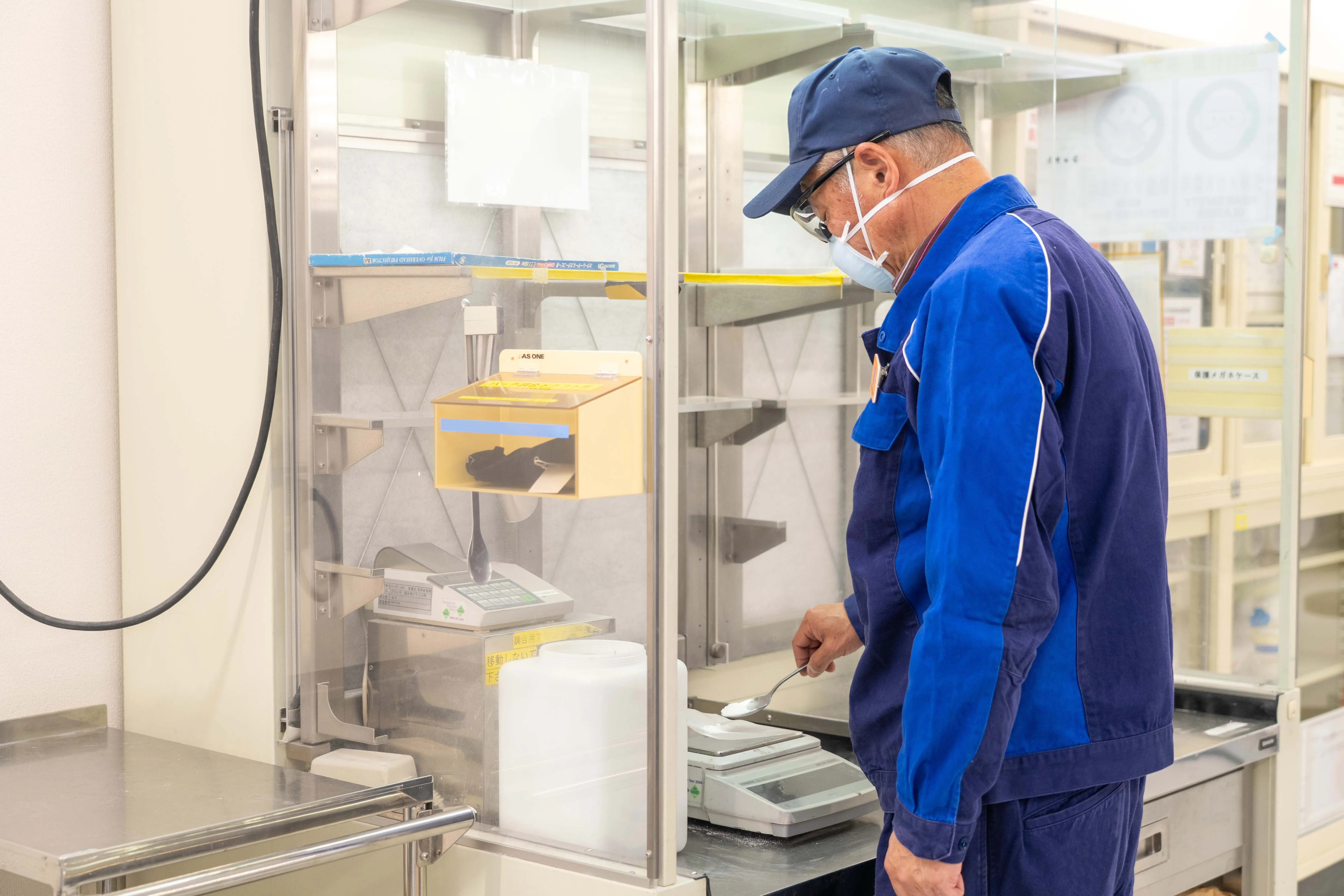
――CRTガラス事業の終盤戦を経験しながら、フラットパネルディスプレイ(FPD)ガラス事業に移っていったのですね。
小森さん「2003年(平成15年)に滋賀高月事業場に異動になり、CRT事業部 製品技術部という部署でディスプレイ用ガラスの材質管理業務に従事しました。この時期は今後CRTからFPDにディスプレイの主役が転換し、FPDガラス事業が大きくなると見込まれていました。
現在はLCDや有機ELがフラットパネルの主流ですが、当時はLCDとPDPがしのぎを削っていました。どちらが主流になるかまだ分からない状況で、当社はLCDとPDP両方のディスプレイ用ガラスを生産していました。
その頃、FPD用ガラスの材質管理はCRT事業部が兼務しており、FPD用ガラス専門の担当者がいませんでした。FPD向けのビジネスが大きくなるのにこれでは良くないということで、FPD専門の担当者として滋賀高月事業場に私が移ったのです。
滋賀高月事業場では、CRT用ガラスを生産する窯が日を追うごとに閉じられていくのを目の当たりにしました。一方でFPD向けのガラスはどんどん生産量が増えていきました。
いま思えばCRTからFPDに上手くバトンタッチできた形ですが、当時の現場では『今後はFPDが売れる』ではなく、『今後はFPDを売っていかなければ仕事がなくなる』という危機感が強かったです。」
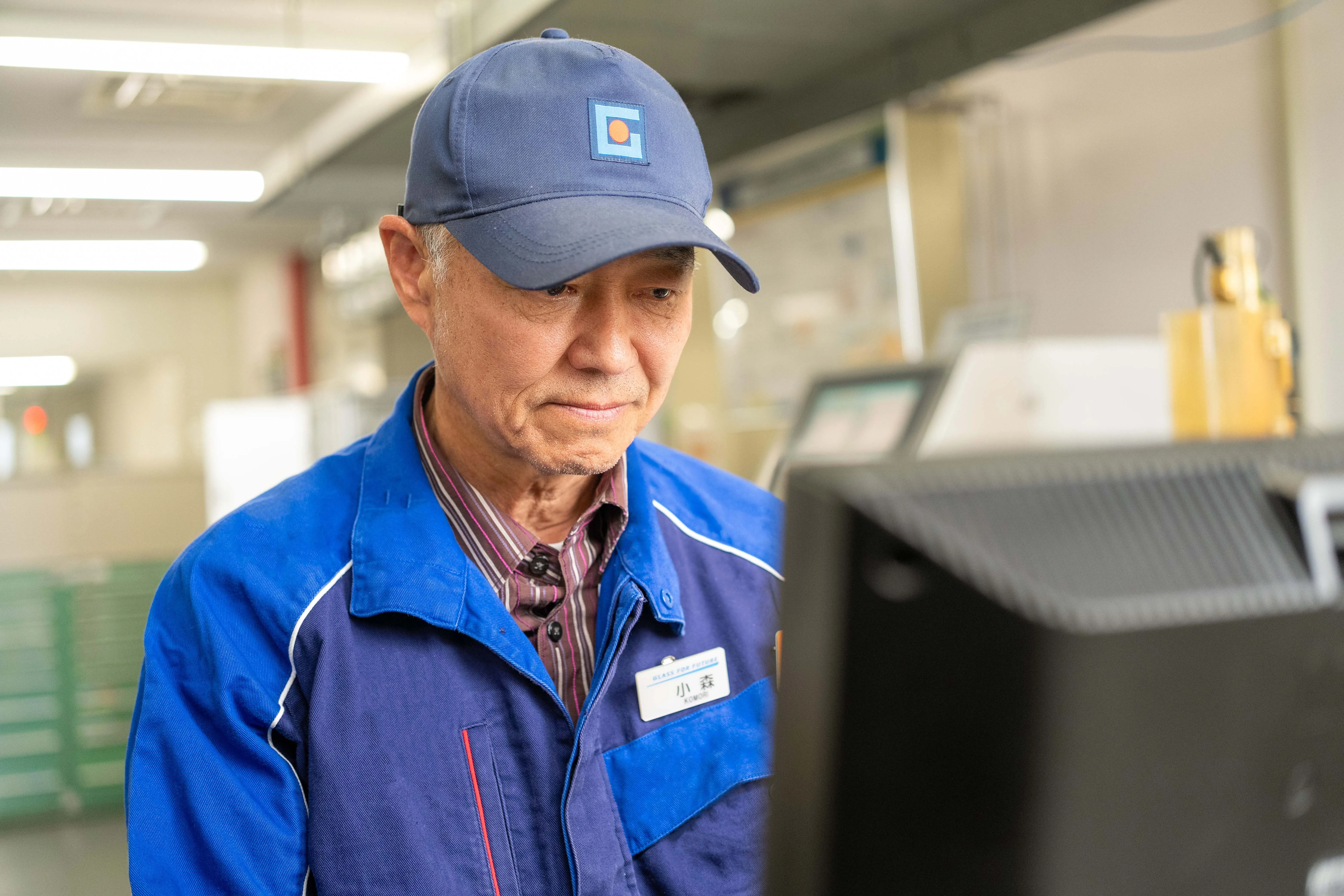
ディスプレイ用ガラス製造に携わる後任を指導する
――小森さんはFPDの現場を見るようになってから部下が増え、役職が上がるに連れて部下の指導が増えていったと思います。近年はディスプレイ用ガラスの製造に携わる後任の指導にも尽力されてきたそうですが、指導のときはどのような点を重視していますか?
小森さん「これまでいろいろな人を指導してきました。新入社員もいたし、他の部署から異動してきた目上の方もいました。さまざまなタイプの人がいて、みんな同じようにやっていては育ちません。1から10まで教えなきゃいけない人もいれば、2まで言えばあとは勝手にわかる人もいます。優秀だと思って放任していると想定外の方向に進んでしまう人もいたので、放任もそうそうできません。しかし、任せなければ本人の自信にもつながりません。後任の指導は難しいと感じました。
指導を重ねるうちに感じたのは、まず相手としっかり対話し、その人の性格や理解のスピードを把握することが大切だということです。一気に教えたほうが良いのか、時間をかけて少しずつ進めたほうが良いのか――指導方法に決まった正解はなく、相手に合わせて柔軟に対応する必要があると実感しました。
若い頃、私は上司が丁寧に根回しをしてくれていたことを強く感じていました。どこかへ話を聞きに行ったり、勉強しに行ったりすると、すでに上司が話を通してくれていて、どの現場でも皆さんが快く教えてくれたのです。その姿勢を見て「自分もこうありたい」と思い、後任のための根回しは私自身も意識して取り組んできました。
現場でガラスの材質や品質を管理するということは、責任が重く、すごくプレッシャーがかかります。良品のガラスが流れていくのは当たり前ではないのです。
窯に原料を入れてガラスとして流出するまでに長くて数週間の時間がかかります。一旦、不良のガラスを流してしまうと、そこから何週間先のガラスまで不良になってしまいかねません。そのプレッシャーに耐えられずに挫けてしまう者もいますし、逆にその重圧を乗り越えると縁の下の力持ちになれたことを実感できてより一層やる気を出す者もいます。」
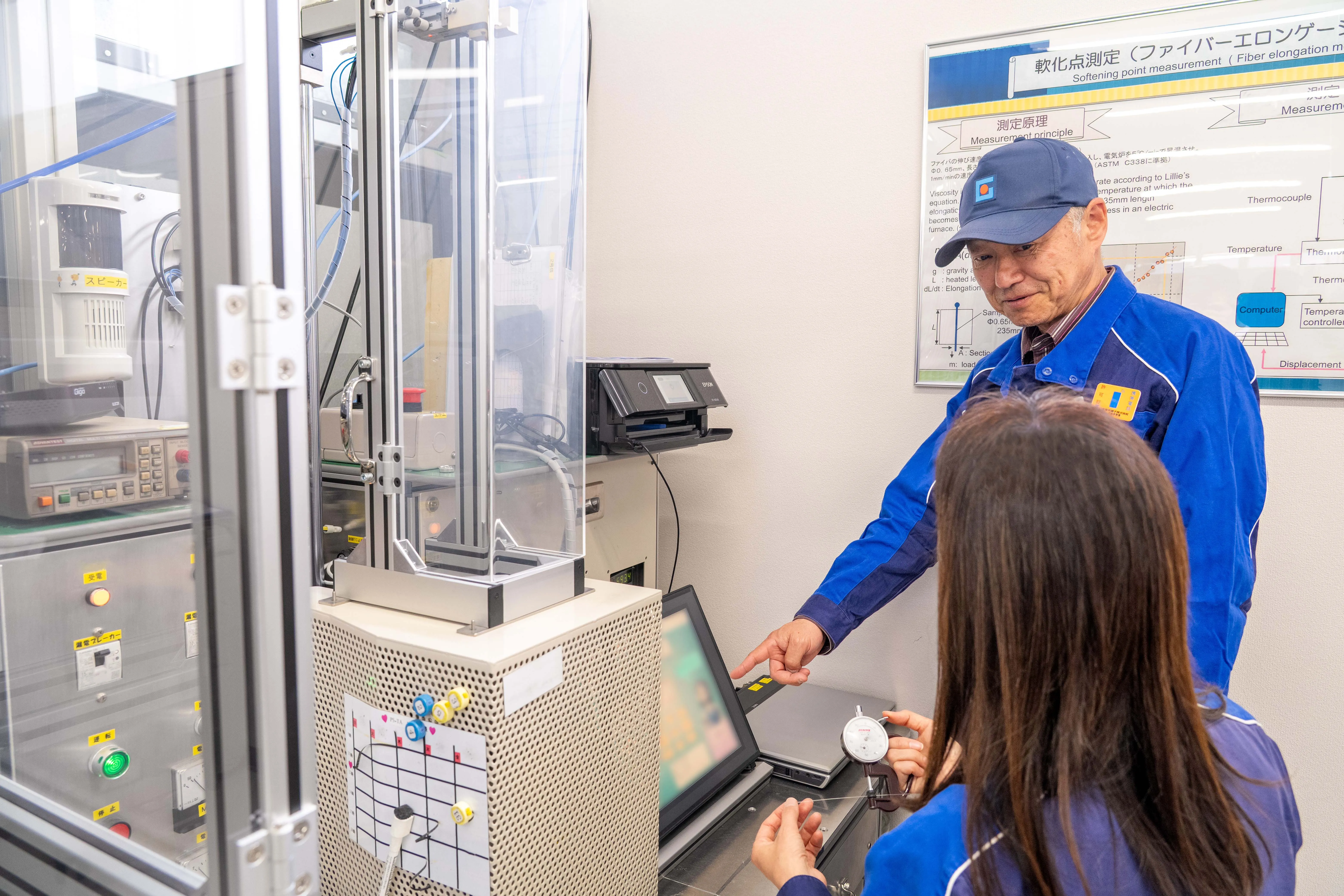
若者には失敗を恐れずにどんどん挑戦してほしい
――キャリアの中で経験した失敗から、どんなことを学びましたか?
小森さん「若い頃は失敗を失敗と思っていませんでした。測定装置を作っていて失敗しても、上司や先輩方は良いところを探してくれて、『ここを使えるんじゃないか』『この部分だけ直したらいいんじゃないか』などと、いろいろ前向きに指導してもらえました。
もちろん、大きなミスも経験しています。かつて、生産したガラスの特性が測定者の人的ミスによってメーカーの要求を逸脱していたにもかかわらず、それに気づかずに出荷してしまい、得意先の工程でトラブルを引き起こしてしまったことがありました。
同じ間違いを二度と起こさないために、人的ミスが起こらないような改善を施しました。当時は、測定者がガラスをバーナーによって手作業で溶かし、決まった形状に成形した後に測定装置で測定するというプロセスでした。しかしこの方法では、人の手が加わる以上、誰が測定するかによって結果にばらつきが出てしまいました。そこで、ガラスを電気融解により自動で溶かして試料片を成形する機構に改良しました。この改良により、外乱の影響を受けず、安定した精度での測定が可能となり、再発防止につながりました。
こうした経験から、ミスを防ぐだけでなく、次につながる前向きな改善を積み重ねていくことの重要性を強く感じました。
――今までの経験が、現在のご自身のキャリアや価値観にどうつながっていますか?
入社して最初にガラスの測定装置の開発に携わり、ガラスの特性も含めて10年くらい学びの期間を過ごしました。そのあと約10年間、CRT用のガラスの組成開発に関わり、そこでも組成の各成分がどんな働きをしているのかといった勉強ができました。
これらの仕事を通して得た測定技術、組成の知識などは、FPD用ガラスの現場での生産活動(材質管理業務)に活かすことができました。全く分野の違う測定と組成の知識や経験が、材質管理業務には必須で、これまで製造現場で材質管理をするために20年かけて訓練してきたかのように思いました。
また、材質管理業務は海外を含めた多くの事業場とかかわりが持てる仕事だったので、顔見知りが増えました。
事業場に行くと、国内外で顔見知りになった人が製造ラインで働いていて声を掛けられるなど、人の縁を感じています。人と人はどこでつながるか分かりません。だからこそ、普段からコミュニケーションを大切にしてほしいです。キャリアも人間関係も、挑戦の積み重ねから広がっていくもの。だから若い人には、失敗を恐れずに一歩踏み出してほしいですね。」
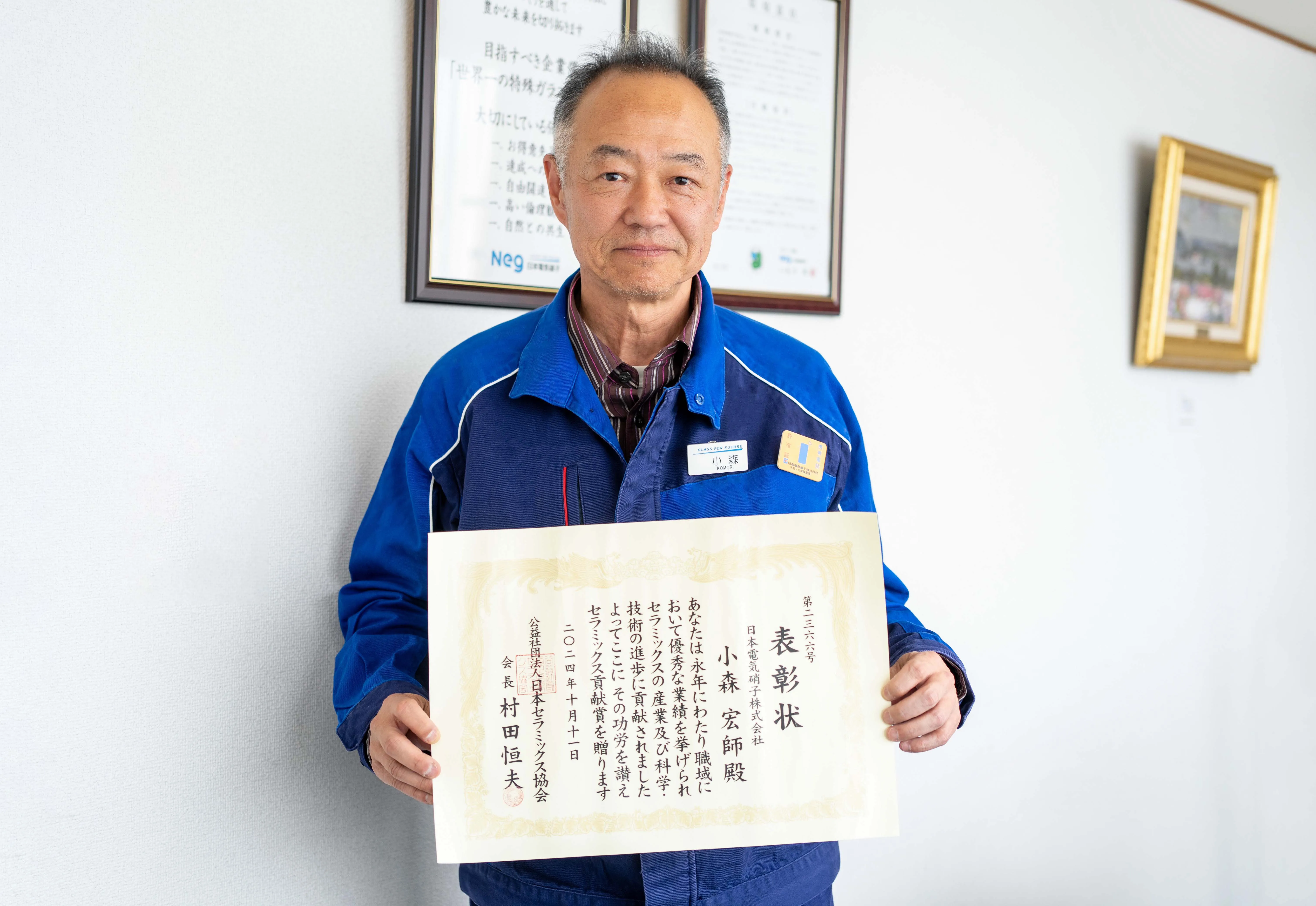
――後任や若手にどのような期待をしていますか。また、未来のNEGをどのように支えてほしいと考えていますか?
小森さん「自分が携わってきた部下達に対しては、いろんなことを経験してほしいです。特に若い方は失敗してもその部署のトップが責任を取ってくれるはずですから、新しいことをどんどん提案して経験すると良いと思います。
ただ闇雲に提案するのではなく、十分に考えを練って『これだけ効率がよくなります』『コストが下がります』と言えるように、いろいろなことを頭に入れてチャレンジしてもらいたいです。
これは現場の人に限らず、NEGで働くすべての若い人に対して言えることです。世の中の役に立つガラスとは、その時代その時代に出てくるものですが、今後はニーズに対していかにタイムリーに応えられるかがビジネスの世界での勝敗を分けることになると思っています。そのスピード感はこれからますます速くなっていくでしょう。世の中のニーズを自分で感じながら新しいガラス組成を開発してほしいです。
当社はメーカーなので利益を上げていかないといけません。新しい組成の開発だけでなく、生産設備の開発も一緒に行う必要があるし、現場はきっちりとオーダーどおりのガラスを作っていかなければなりません。新しいものにチャレンジして、世の中に貢献できるガラスを作ってほしいです。」
――ありがとうございます。
イノベーションは既存の技術や知識の先にある
セラミックス貢献賞の技能部門の受賞者と聞いて、NEGを代表するガラス製品の開発者や新技術の開発でガラス業界をリードした研究者をイメージした人から見ると、小森さんの経歴は縁の下の力持ちと呼ぶにふさわしく、少し意外に感じたのではないでしょうか。
小森さんは入社直後から上司に教えを受け、まったく新しいものを開発するというより、上司のやってきたことを引き継いで改良・発展することやコストダウンすることから仕事を始めたと述べました。
この話からは測定技術の自社開発や製造工程の最適化の実現には、基礎をしっかり学んだことが背景としてあることが伺えます。また、NEGが擁するさまざまな経験を積んだ技術者が、何もないところからイノベーションを生むのではなく、既存の技術や知識を活かして技術を堅実に進化させていることも伝わってきます。
さらにNEGでは技術者が一つの技術を極めることよりも、多くの経験を積んで広い視野と深い造詣を併せ持つように成長を導かれていることも垣間見えました。小森さんの薫陶を受けた技術者は次の世代をリードし、さらにその次の世代の人材を育成し続けます。小森さんの話を通じて、NEGが今後も競争力をさらに高め、ガラスを含めたセラミックス業界全体の発展にますます貢献していくことが確信できたのではないでしょうか。
用語解説
-
ブラウン管(Cathode Ray Tube)の略。1950年頃から2000年頃まで世界の画像表示装置の中心だった。
-
液晶ディスプレイ(Liquid Crystal Display)の略。2000年代にブラウン管に代わりディスプレイの主役となった。スマホなどのモバイル機器、PCのモニターなどに用いられる。
-
プラズマディスプレイパネル(Plasma Display Panel)の略。大画面に強い薄型ディスプレイとして1990~2000年代に普及したが、現在は液晶や有機ELに置き換わり、ほとんど生産されていない。
-
フラットパネルディスプレイ(Flat Panel Display)の略。CRT(ブラウン管)に代わる、薄型で、平坦な画面の薄型映像表示装置の総称。