Diversity and Inclusion
Hiring a Diverse Workforce
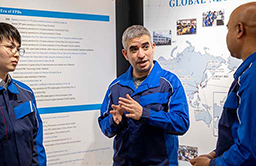
We believe that employees are the foundation of a company’s growth and accordingly hire a diverse range of human resources regardless of their gender, age, nationality, or other characteristics. We are also increasing the hiring of recent graduates and incorporating new recruiting methods and approaches. For example, we hire highly qualified, mid-career professionals and young professionals changing careers. We also make use of referral recruitment when hiring employees locally. Even amidst accelerating job mobility, we are creating a wide range of entry points, such as for previous NEG employees to be rehired, to help us in securing a diverse workforce.
We are also a proactive employer of people with disabilities. In 1980, we established a special-purpose subsidiary aimed at employing people with disabilities. We were among the first six companies in Japan to do so. Since then, we have sought to increase our employment rate for people with disabilities to 4.6%, far above the statutory requirement of 2.5%, and have hired people with disabilities as full-time employees. Moving forward, we will continue to employ people with disabilities.
Hiring Mid-Career Professionals
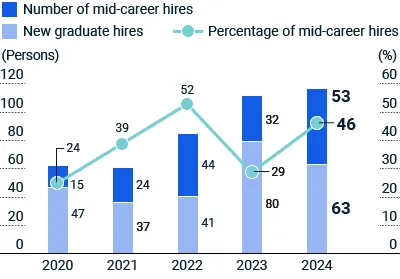
We strengthen our foundation of human resources by actively hiring mid-career professionals.
In addition to recruiting new graduates and other outstanding talent for the future, we hire experienced professionals with specialized expertise and a strong sense of professionalism. We will continue pursuing individuals with diverse experiences and skills, to bolster our ranks of human resources capable of leading in our business expansion.
Creating a Thriving Environment for a Diverse Workforce
In addition to our continued commitment to providing employment for people with disabilities, we also strive to cultivate a work environment in which the diverse values and backgrounds of employees, regardless of gender, age, nationality, and gender identity, are respected and in which employee welfare and happiness are prioritized.
Workplace Improvement Examples
-
Disabled: Expanding employees’ scope of work; installing wheelchair ramps, elevators, and accessible washrooms
-
Women: Providing childcare support (received Platinum Kurumin accreditation), creating more in-house support systems, and holding events for female employees to exchange opinions
-
Seniors: Initiating a stepped system for raising the pay of rehired workers, and establishing compensation systems that match job duties
-
Foreign nationals: Following up to ensure they understand company systems, holding training and Japanese language classes, mentoring them
-
LGBTQ persons: Raising LGBTQ awareness during human rights education, making things less gender-based (gender-free uniforms, changing rooms, washrooms)
Employment of People with Disabilities
(NEG and consolidated subsidiaries in Japan)
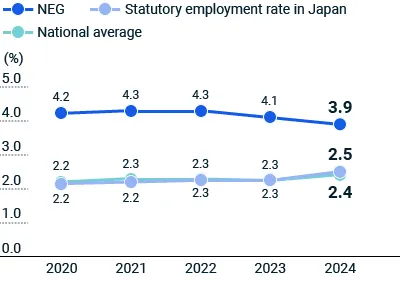
Our special-purpose subsidiary E.G. UNIVERSUPPORT CO., LTD. (https://www.us-neg.com/) employs person with disabilities. In 2018, the company became the second special-purpose company to receive Youth Yell Certification from the Ministry of Health, Labour and Welfare for outstanding action in hiring and training young people. In fiscal 2021, the company received Monisu Certification as a small- and medium-sized business with excellent employment for persons with disabilities.
In April 2024, we set a target to increase the percentage of people with disabilities in our workforce to 4.6%, which is above the statutory requirement of 2.5%.
At the end of 2024, we maintained a 3.9% employment rate for people with disabilities, slightly down from the previous year due to some employees reaching mandatory retirement age. We will continue actively engaging people with disabilities as valued members of our workforce.
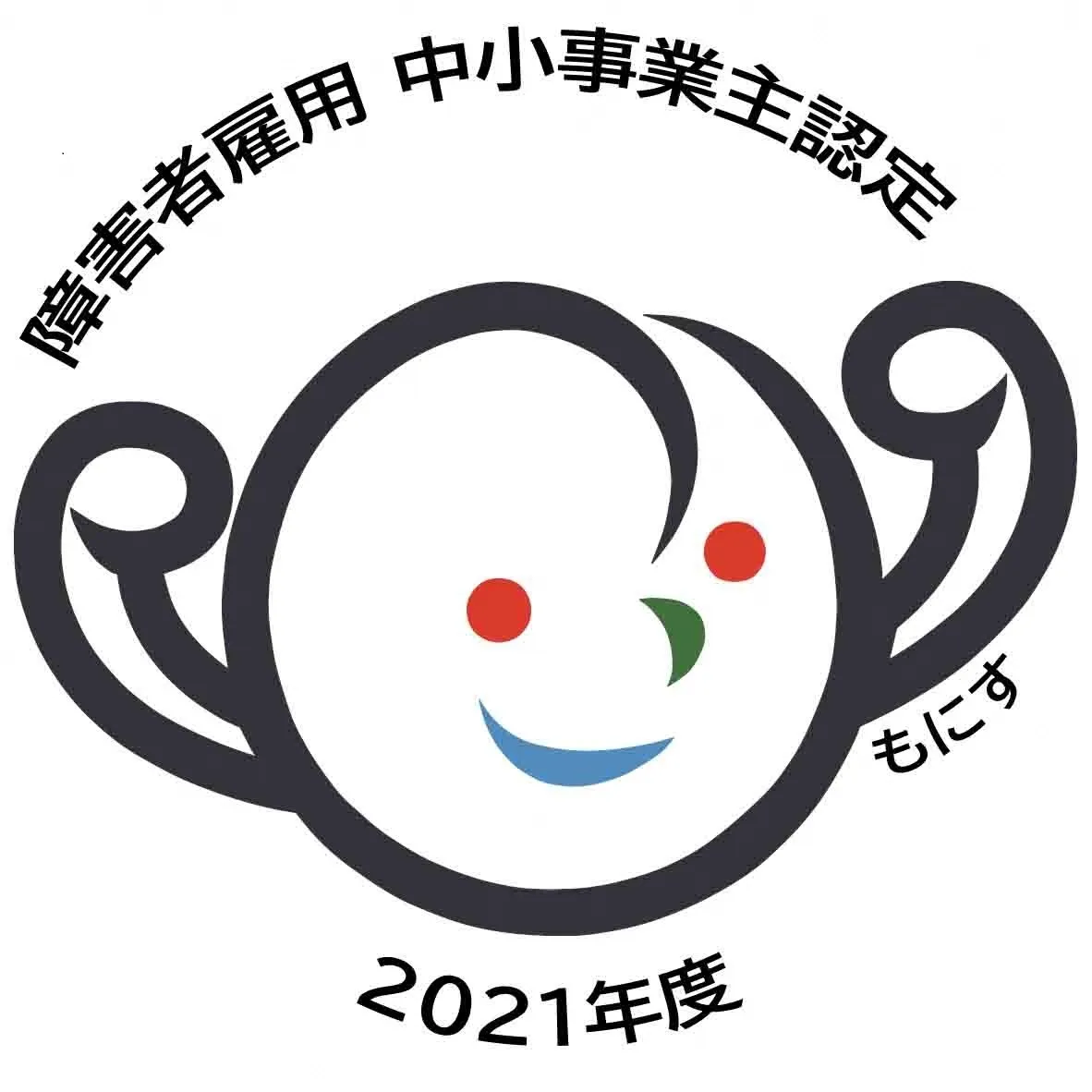
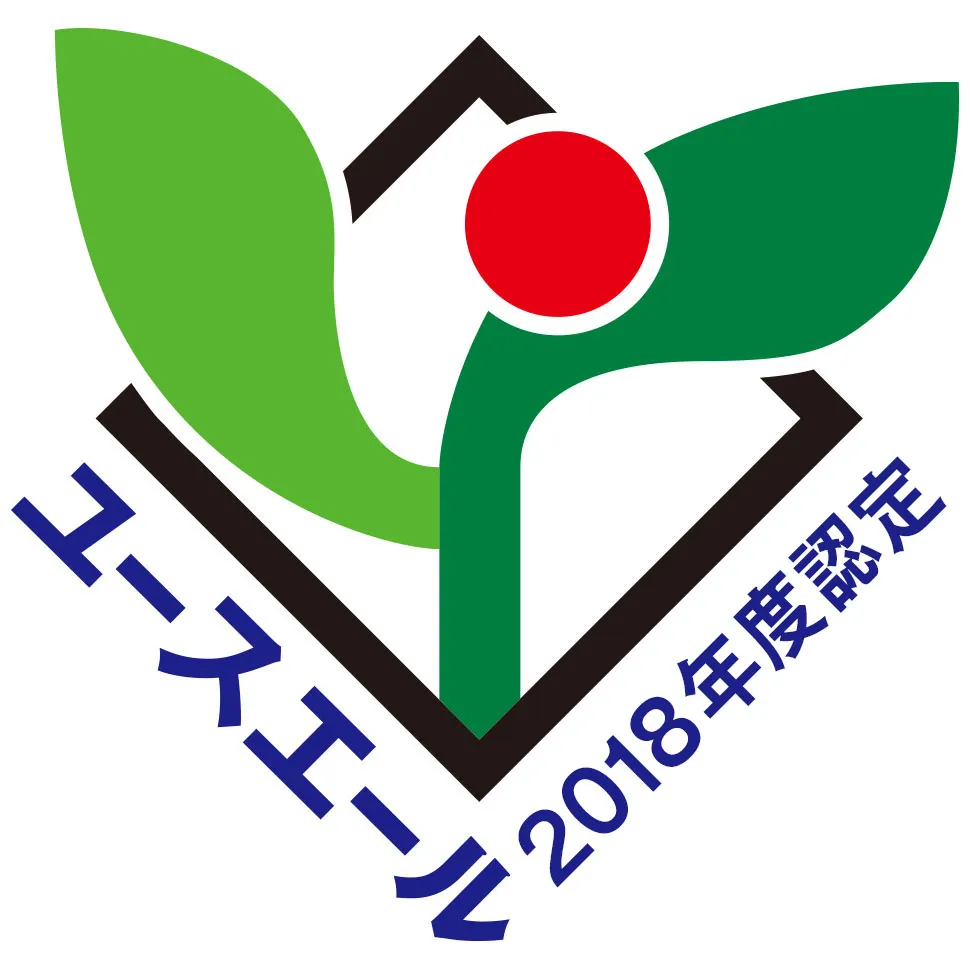
Aiming to exceed the statutory requirement with 4.6% employment of persons with disabilities
Learn more about the efforts of E.G.UNIVERSUPPORT CO., LTD.
Promoting the Active Participation of Senior Professionals
Securing and actively leveraging the expertise and abilities of senior professionals is becoming increasingly essential. Following the recent changes to laws and the social trends regarding the employment of older individuals, we have set up a system for gradually increasing senior employee compensation levels in accordance with their volume and evaluation of their work. We wish to further utilize motivated and capable seniors and promote a smooth handoff to the younger generation.
Empowering Employees with Roots in Other Countries
As the number of our non-Japanese employees increases, we are providing follow-up support to ensure their understanding of the company’s policies, and supporting their smooth workplace communications through measures such as Japanese language classes and a mentoring system.
In October 2019, we promoted the first foreign national employee to the position of manager, and have promoted more since then. In January 2023, we appointed a foreign national employee of an overseas subsidiary as an executive officer at the head office for the first time. Going forward, we will be putting energy into ensuring that workplace environments allow employees of many different backgrounds to participate in the workplace with vitality, building synergy through mutual respect for each other’s culture.